How to Convert Your Art Into a Print-Ready DTF File
If you're looking to turn your artwork into print-ready DTF transfers, you're in the right place. DTF printing, or Direct to Film printing, is a popular method for transferring designs onto fabrics. But getting your digital art ready for this process can be tricky. In this guide, we’ll walk through the essentials to ensure your art looks great and prints perfectly. From understanding the basics to preparing your files, let's dive in!
Key Takeaways
- DTF printing uses water-based inks for vibrant and durable designs.
- Always use high-resolution images (at least 300 DPI) for the best results.
- Choose the right file format, like PNG or vector files, to maintain quality and transparency.
- Avoid small details and large solid areas in your designs to enhance print quality.
- Conduct test prints to identify issues before final production.
Understanding DTF Printing Basics
So, you're thinking about getting into DTF printing? Awesome! It's a cool way to get your designs onto all sorts of stuff. Let's break down the basics so you know what you're getting into.
What Is DTF Printing?
Okay, so what is DTF printing anyway? DTF stands for Direct to Film. Basically, you print your design onto a special film, and then you transfer that design onto whatever you want – shirts, bags, you name it. It's different from other methods because it works on lots of different materials, and the prints are pretty durable. This DTF printing method is becoming super popular because it's versatile and the results look great.
Benefits of DTF Transfers Ready to Press
Why go with DTF transfers? Here's the lowdown:
- Versatility: You can use DTF on cotton, polyester, blends – pretty much anything. That's a big win compared to some other printing methods.
- Durability: DTF prints hold up well after washing, so your designs won't fade or crack easily.
- Vibrant Colors: DTF gives you really bright, eye-catching colors that pop.
DTF printing is a game-changer because it lets you print detailed, full-color designs without a ton of setup. Plus, you don't have to worry about pre-treating fabrics like you do with some other methods. It's a more straightforward process overall.
Key Components of DTF Printing
To get started with DTF, you'll need a few key things:
- DTF Printer: This is the heart of the operation. It's a special printer that uses DTF inks.
- DTF Inks: These are pigment-based inks designed specifically for DTF printing. They're what give you those vibrant colors.
- DTF Film: This is the special film you print your design onto. It's coated to accept the ink and release it onto the fabric.
- DTF Powder: This is a special adhesive powder that helps the ink bond to the fabric. You apply it to the printed film before heat pressing.
- Heat Press: You'll need a heat press to transfer the design from the film onto your final product.
Component | Function |
---|---|
DTF Printer | Prints the design onto the film |
DTF Inks | Provides the color for the print |
DTF Film | Holds the design during transfer |
DTF Powder | Adheres the ink to the fabric |
Heat Press | Transfers the design to the final product |
Preparing Your Digital Artwork for Print
Okay, so you've got your design idea, that's awesome! But before you just send it off to be printed, there are a few things you really need to do to make sure it comes out looking great. It's like baking a cake – you can't just throw everything in and hope for the best. You need to prep! Let's walk through the steps to get your digital artwork ready for DTF printing.
Choosing the Right File Format
First things first, let's talk file formats. This is super important. You can't just use any old image file and expect amazing results. Think of it like this: some file formats are like blurry photos, and others are super sharp. For DTF, you want sharp! The best options are usually vector files (like AI or SVG) or high-resolution raster files (like PNG). Vector files are great because they can be scaled up or down without losing quality. Raster files, on the other hand, are made up of pixels, so you need to make sure they're high resolution from the start.
- Vector (AI, SVG): Scalable, best for logos and graphics with clean lines.
- Raster (PNG, TIFF): Use PNG to preserve transparency, TIFF for very high quality (but larger file sizes).
- Avoid: JPEG (can introduce artifacts and loss of quality).
Setting Up Image Resolution
Resolution is key! If your image resolution is too low, your print will look blurry and pixelated. No one wants that! The general rule of thumb is to aim for at least 300 DPI (dots per inch). This means that there are 300 tiny dots of ink for every inch of your image, which gives you a nice, crisp print. You can check the resolution of your image in Photoshop or any other image editing software. Just go to Image > Image Size and take a look. If it's below 300 DPI, you might need to find a higher resolution version of your image or recreate it.
Color Management for DTF Printing
Color management can be a bit tricky, but it's worth getting right. Basically, it's all about making sure the colors you see on your screen are the same colors that get printed on your shirt. The best way to do this is to work in the CMYK color mode. CMYK stands for Cyan, Magenta, Yellow, and Key (Black), and it's the color mode that printers use. If you design in RGB (Red, Green, Blue), which is what most screens use, the colors might shift when they're printed. To convert your image to CMYK in Photoshop, go to Image > Mode > CMYK Color. Keep in mind that some colors look different in CMYK than they do in RGB, so you might need to make some adjustments to get the look you want.
It's a good idea to do a test print before you commit to a large run. This will give you a chance to see how the colors look and make any necessary adjustments. Nothing is worse than printing 100 shirts and realizing the colors are all wrong!
File Preparation and Formatting
Alright, so you've got your design ready to go. Now comes the part where we make sure it's actually ready for the DTF printer. This is more than just hitting 'print'. It's about making sure the file is set up in a way that the printer can understand and reproduce accurately. Trust me, a little prep here saves a lot of headaches later.
Selecting the Ideal File Type
Choosing the right file type is super important. For DTF, you've got a couple of good options, but vector files are generally the way to go. Think .ai
, .eps
, or .svg
. Why? Because they're scalable. You can resize them without losing quality, which is a lifesaver if you're printing the same design on different sized items. Raster files like .jpg
or .png
can work, but you need to make sure they're high-resolution from the start. Otherwise, you'll end up with a blurry, pixelated mess. If you are using raster files, make sure you have a high image resolution.
Ensuring Transparency in Your Design
Transparency is key for DTF. You don't want a big, ugly box of white (or any other color) around your design when it's printed on your garment. Your design needs to have a transparent background so that only the actual design shows up. Most design software lets you easily remove backgrounds. In Photoshop, the Magic Wand tool is your friend. Just select the background and delete it. You should see that checkerboard pattern indicating transparency. If you're working with more complex designs, you might need to use the Select and Mask feature to really refine those edges. Remember to check for transparency in your design before sending it to print.
Document Setup for Optimal Results
Setting up your document correctly from the start can save you a ton of time and frustration. Here's a few things to keep in mind:
- Size Matters: Make sure your document size matches the size you want your print to be. Don't try to scale up a small document to a large print size – it'll look terrible.
- Resolution is Key: Aim for at least 300 DPI (dots per inch). This ensures that your print will be sharp and detailed. Lower resolutions will result in blurry prints.
- Color Mode: CMYK is generally the way to go for DTF printing. This color mode is designed for printing, and it'll give you the most accurate color reproduction. Convert your image to CMYK early in the process to avoid any surprises later on. You can always adjust colors in CMYK if needed.
Proper document setup is the foundation for a successful DTF print. Taking the time to get it right will pay off in the end with a high-quality, professional-looking product.
Here's a quick table summarizing the key document setup settings:
Setting | Recommendation |
---|---|
File Type | Vector (.ai, .eps, .svg) preferred, Raster (.png, .jpg) acceptable (300 DPI+) |
Transparency | Required |
Resolution | 300 DPI minimum |
Color Mode | CMYK |
Avoiding Common Design Pitfalls
DTF printing is awesome, but it's easy to mess things up if you're not careful. There are some common design mistakes that can really impact the quality and how long your prints last. When you're setting up your file in Photoshop or Illustrator, keep these things in mind to get the best results. It's all about avoiding those little things that can ruin an otherwise great design.
Steering Clear of Small Details
Tiny details, dots, and thin lines are a DTF printer's worst nightmare. They just don't hold up well over time and can start peeling off, which ruins the whole print. Think about it – those little specks of ink have a hard time sticking around. It's better to go with bolder, more solid elements that will stay put.
Managing Solid Print Areas
Big, solid areas of ink might look cool, but they can make the garment super uncomfortable. No one wants to wear a shirt that feels like a plastic sheet. Plus, these areas can crack and peel more easily. It's all about finding a balance between a cool design and a wearable product. Consider incorporating breathable elements into your design to avoid this issue.
Incorporating Negative Space
Using negative space is a great way to make your design pop and keep it breathable. It also helps to avoid those big, solid areas that can be problematic. Think about how you can use the absence of ink to create interesting shapes and patterns. It can really elevate your design and make it more comfortable to wear.
It's important to remember that DTF printing isn't just about slapping a design on a shirt. It's about creating something that looks good, feels good, and lasts. By avoiding these common pitfalls, you can make sure your prints are top-notch.
Optimizing Image Quality
Using High-Resolution Images
Using high-resolution images is super important for DTF printing. You want your prints to look crisp and professional, right? So, starting with a good quality image is key. Think about it like this: if you start with a blurry photo, it's just going to look even worse when it's printed on fabric. Aim for at least 300 DPI optimal resolution guidelines to avoid pixelation and ensure all the details show up clearly.
Working in CMYK Color Mode
Working in CMYK color mode is a must. Here's why:
- CMYK is the standard color model for printing. Your computer screen uses RGB, which can display a wider range of colors than a printer can reproduce.
- Converting to CMYK early in the design process lets you see how the colors will actually look when printed, preventing unwanted surprises.
- Use the Info Window to spot-check your colors and see if they’re within the CMYK range. If an exclamation point appears next to the CMYK values, you’ve got an out-of-gamut color that could shift when printed.
It's a good idea to convert your design to CMYK before you finalize it. This way, you can make any necessary adjustments to the colors to ensure they look their best in the final print.
Refining Edges and Backgrounds
Cleaning up those edges can make a world of difference. After removing the background, you might notice some rough, pixelated edges. This is where edge refinement comes in handy:
- With your selection still active, go to Select > Modify > Expand and choose 1-2 pixels.
- Click Delete again to remove any stray pixels.
- If the edges still look jagged, manually going in with the Eraser Tool or even redrawing parts of the design may be necessary.
Choosing Suitable Design Elements
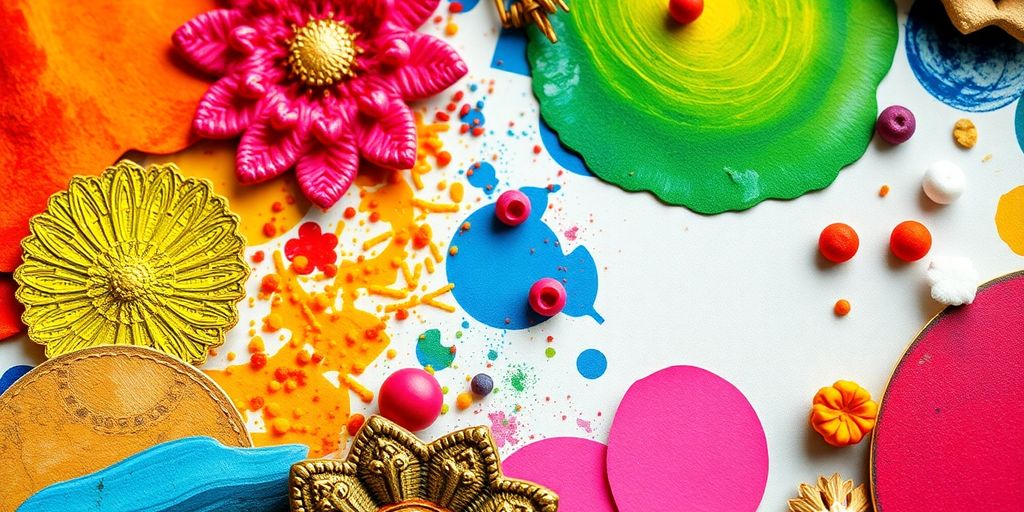
When it comes to DTF printing, not all designs are created equal. You really need to think about what elements will work best with the process. It's not just about what looks good on your screen; it's about what will translate well onto fabric. Let's get into it.
Incorporating Breathable Elements
One of the biggest things to keep in mind is breathability. Large, solid areas of ink can make a garment uncomfortable to wear. Think about it – a big, thick patch of ink isn't going to let air through. So, how do you avoid this?
- Use see-through elements in your design. This doesn't mean making parts of your design transparent, but rather incorporating elements that allow the fabric to breathe.
- Consider using distressed textures or patterns. These can add visual interest without completely blocking airflow.
- Incorporate negative space strategically. This can break up large blocks of color and improve breathability.
It's a good idea to think about the end user. Are they going to be wearing this shirt while working out? Or is it just for casual wear? This will influence how much breathability you need to consider.
Maintaining Crisp Edges
DTF printing works best with crisp, clean edges. Soft or blurry edges can end up looking muddy or undefined. This is because the ink dots need a solid surface to adhere to. Here's what to keep in mind:
- Use vector graphics whenever possible. Vector graphics are made up of mathematical equations, so they can be scaled without losing quality.
- If you're using raster images, make sure they have a high resolution (300 DPI or higher).
- Avoid using anti-aliasing on your edges. Anti-aliasing is a technique that smooths out edges by adding slightly blurred pixels, but this can cause problems with DTF printing.
Balancing Color and Contrast
Color and contrast are key to making your designs pop. But it's important to strike the right balance. Too much contrast can make your design look harsh, while too little can make it look washed out. Here are some tips:
- Use a color palette that is visually appealing and appropriate for your design. There are many online tools that can help you create a cohesive color palette.
- Adjust the contrast of your image to make sure that the colors are vibrant and distinct. You can do this in Photoshop or another image editing program.
- Consider using a color profile that is specifically designed for DTF printing. This can help ensure that your colors are accurate and consistent.
When prepping artwork for DTF, having rich blacks and bright whites can make a world of difference. Remember to choose your file formats wisely!
Testing and Adjusting Your DTF Transfers
So, you've prepped your files, designed your masterpiece, and you're ready to print. Awesome! But before you go into full production mode, it's super important to test your DTF transfers. This step can save you a ton of headaches (and money) in the long run. Let's get into it.
Conducting Test Prints
Okay, first things first: test prints. Don't skip this! Print a small version of your design on the actual fabric you'll be using for your final product. This helps you see how the colors look, how well the design adheres, and if there are any weird issues you didn't catch on screen. Think of it as a dress rehearsal for your design. It's better to catch a problem now than to ruin a whole batch of shirts later. I usually do a few different test prints with slight variations in settings to see what works best. It's a bit of trial and error, but totally worth it. Remember to prepare your digital artwork correctly.
Identifying Common Issues
Alright, you've got your test print. Now it's time to play detective. Here are some common problems to look out for:
- Color Issues: Are the colors accurate? Do they look washed out or too vibrant?
- Adhesion Problems: Is the design peeling or cracking after pressing?
- Detail Loss: Are fine lines or small details disappearing?
- Weird Textures: Does the print feel rough or uneven?
If you spot any of these, don't panic! It just means you need to tweak your settings. Keep a log of each test print and the issues you find. This will help you track your progress and figure out what adjustments you need to make. I find it helpful to take pictures of each test print so I can compare them side-by-side.
Making Necessary Adjustments
So, you've identified some issues. Now what? Time to adjust! Here's a quick rundown of common fixes:
- Color Issues: Adjust your color profile in your design software. Make sure you're working in CMYK. Also, check your printer settings to ensure the correct color profile is selected.
- Adhesion Problems: Increase the pressure or temperature on your heat press. Also, make sure you're using the correct pressing time. Different fabrics may require different settings.
- Detail Loss: Increase the resolution of your image. Also, make sure your design doesn't have any super-fine lines that are too thin to print properly.
- Weird Textures: Adjust the amount of ink being laid down. Too much ink can cause a thick, uneven print. Also, make sure your heat press is applying even pressure across the entire design.
Don't be afraid to experiment! DTF printing can be a bit finicky, and it may take some time to dial in the perfect settings for your specific printer, ink, and fabric. The key is to be patient, methodical, and to keep good records of your tests. You'll get there!
Here's a simple table to help you keep track of your adjustments:
Issue | Possible Solution(s) |
---|---|
Color off | Adjust color profile, check ink levels |
Poor adhesion | Increase pressure/temp/time, try different transfer film |
Detail lost | Increase resolution, simplify design |
Uneven texture | Reduce ink, ensure even pressure |
Wrapping It Up
So there you have it! You’re now ready to turn your artwork into a print-ready DTF file. Just remember to keep things straightforward, use high-quality images, and pay attention to color management. Always check your file formats and look out for common mistakes before hitting print. With a bit of practice, you’ll get the hang of DTF printing in no time. Soon enough, you’ll be creating awesome prints that you can be proud of. Happy printing!
Frequently Asked Questions
What software do I need for DTF printing?
You'll need design software like Adobe Illustrator or CorelDRAW for DTF printing. If you're on a budget, online design tools can also work. You might also need skills in photo editing and color management.
How do I get my digital artwork ready for print?
To prepare your artwork for print, focus on high resolution, the right file formats, and managing colors well. Make sure you understand the difference between vector and raster graphics.
What materials do I need to create my own DTF transfers?
To make DTF transfers, you'll need special inks, the right preparation for your materials, and the correct types of media. Ensure your designs are high resolution and that you manage colors carefully.
Is RGB or CMYK better for DTF printing?
For DTF printing, CMYK is the best choice because it provides accurate color representation. Make sure your file type matches your printer’s requirements.
How can I improve the quality of my DTF prints?
To enhance print quality, use high-resolution images, work in CMYK color mode, and refine edges and backgrounds. This ensures your prints look sharp and vibrant.
What should I avoid when designing for DTF printing?
Avoid small details, large solid areas, and gradients in your designs. These can lead to issues like peeling or a less breathable fabric, affecting the final product.